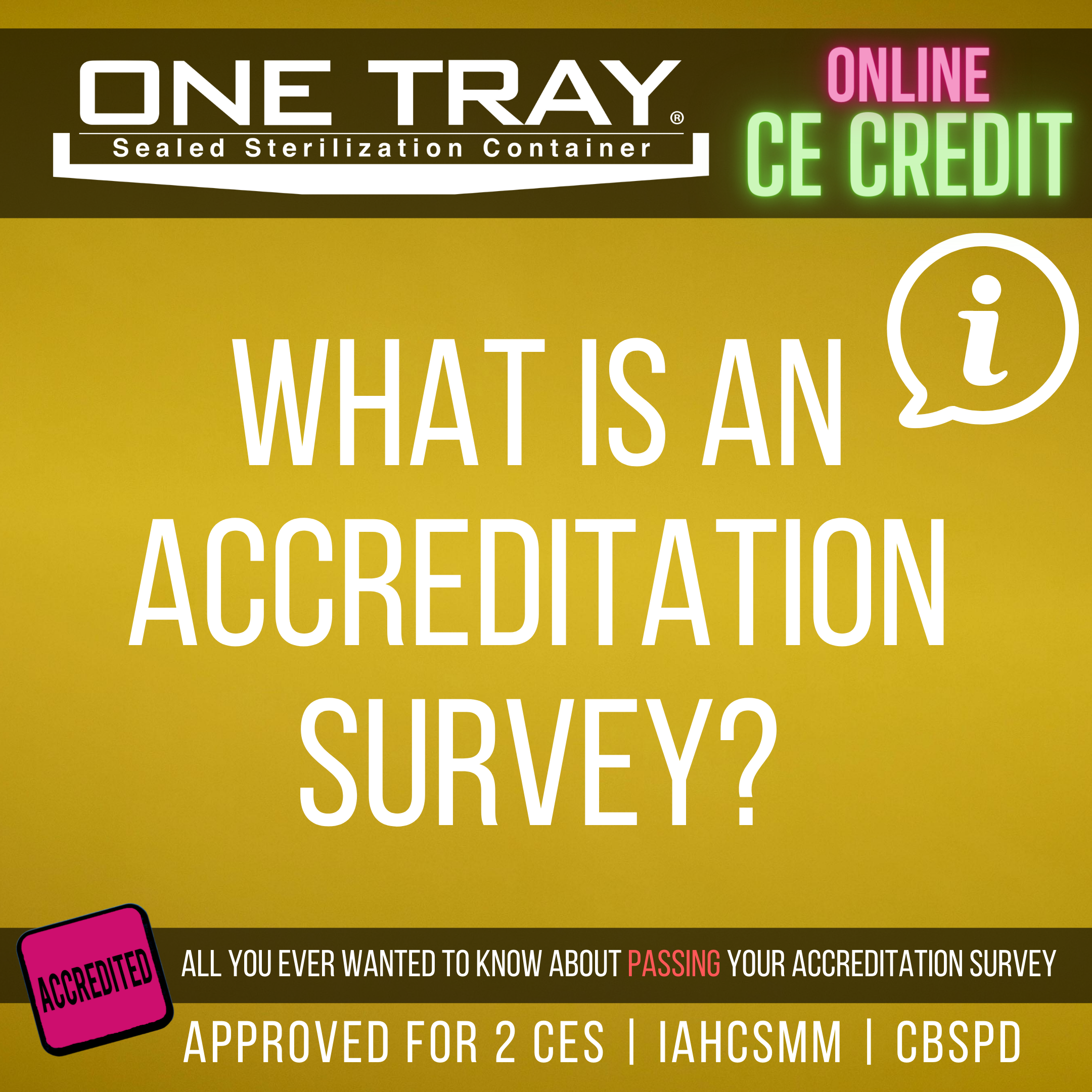
1. What is an Accreditation Survey?
Accreditation of healthcare facilities involves an on-site survey to assess compliance with standards. A team of surveyors will be sent to the facility and will evaluate its practices according to industry standards. The facility will be scored according to their performance in relation to those standards. Each accreditation agency uses a decision tree on how to rate compliance with a standard. Achieving accreditation can benefit the facility by improving patient safety and reducing risk, by meeting some states’ requirements for accreditation, by meeting some insurance providers’ requirements for accreditation, and by strengthening and maintaining the organization’s performance excellence.
Many Accreditation surveys are conducted on a cycle of every 3 years, although some agencies may require an interim survey if there were deficiencies that should be rechecked.
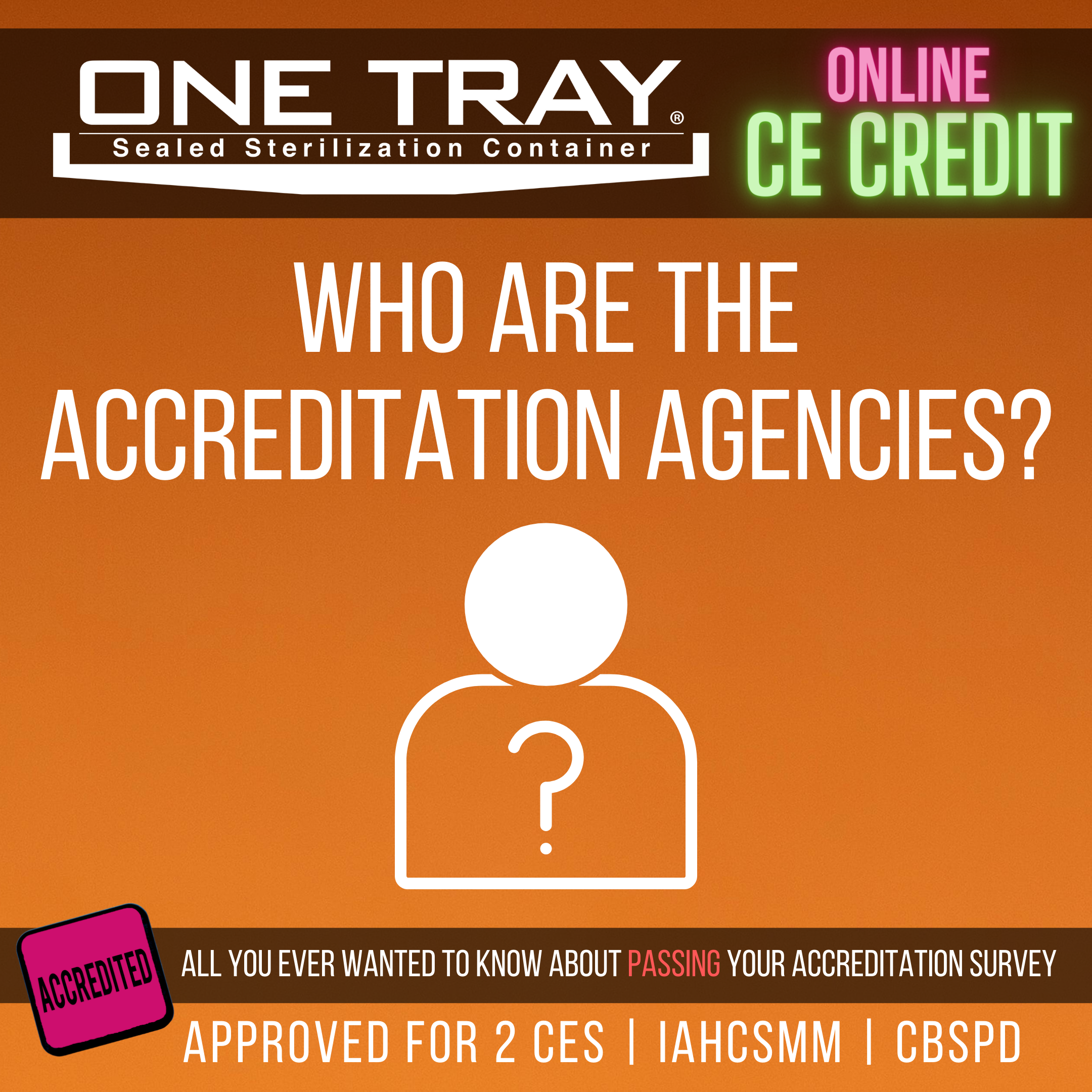
2. Who Are the Accreditation Agencies?
These are the most well known accreditation agencies in the United States. The particular agency you are likely to encounter will depend upon the type of facility in which you work. Click the links for more information on each organization.
Ambulatory:
- AAAHC (Association for the Accreditation of Ambulatory Healthcare) Founded in 1979, with over 6,100 facilities accredited. – https://www.aaahc.org/
- AAAASF (American Association for Accreditation of Ambulatory Surgery Facilities) Founded in 1980. –https://www.aaaasf.org/
Hospital and Ambulatory:
- TJC (The Joint Commission) Founded in 1951, with over 22,000 facilities accredited. – https://www.jointcommission.org/
- HFAP (Healthcare Facilities Accreditation Program) Founded in 1945.- https://www.hfap.org/
Hospital:
- DNV-GL (Det Norske Veritas) Founded in 1864, with over 600 US facilities accredited. –https://www.dnvgl.com/

3. Are Accreditation Surveys Required or Voluntary?
Accreditation agencies are not regulatory in and of themselves, and so participation in Accreditation surveys are voluntary by nature. There are two circumstances in which Accreditation surveys are not voluntary:
- In order to participate in and receive federal payment from Medicaid and Medicare, a healthcare organization must meet government requirements for program participation. This certification is achieved by a survey conducted by CMS, or by another accrediting organization that has contracted with them to perform surveys that meet or exceed Medicare’s requirements (a process called “deeming”). These “deemed status” surveys are regulatory because they represent certification by CMS.
- Many states are now requiring Accreditation.
In addition to these reasons, many private insurers are now requiring Accreditation for payment. This puts tremendous financial pressure on the healthcare organization to voluntarily participate in an Accreditation survey.
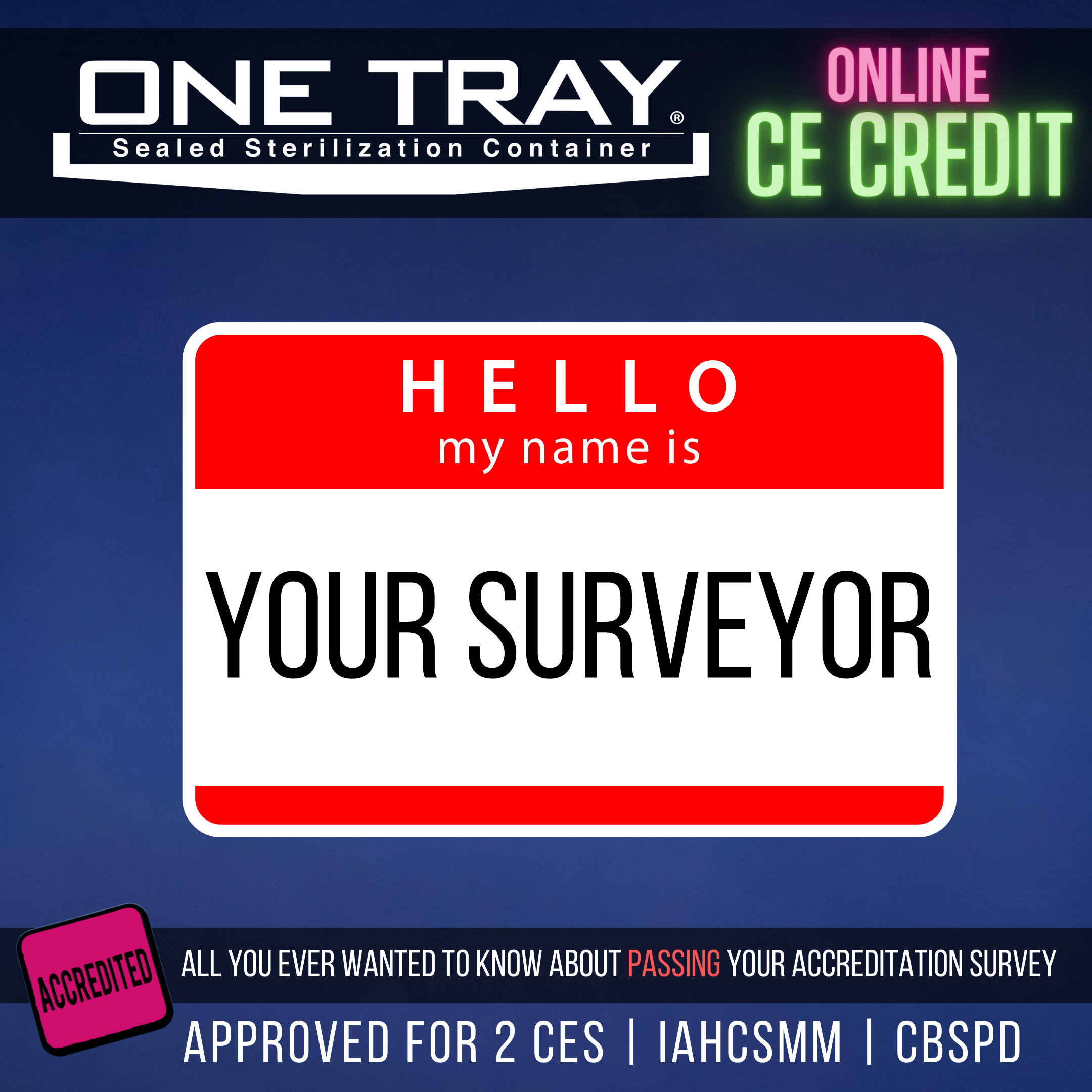
4. Profile of a Surveyor
When it comes time for a survey, there will typically be a team of surveyors that come to the facility. The number of surveyors is based upon the size and complexity of the organization being surveyed. The surveyors who come will have a broad variety of backgrounds, including both clinical and administrative experience. Typically the team will try to match the surveyor’s background to the areas they will survey, but this is not perfectly applied. It is uncommon to have surveyors with direct experience working in a Sterile Processing Department, unless an Infection Preventionist or Nurse had prior experience managing or working in Sterile Processing. Most often, Sterile Processing will be matched with a surveyor with experience in or around the Operating Room (such as a physician or an OR Nurse), but with limited experience with Sterile Processing.
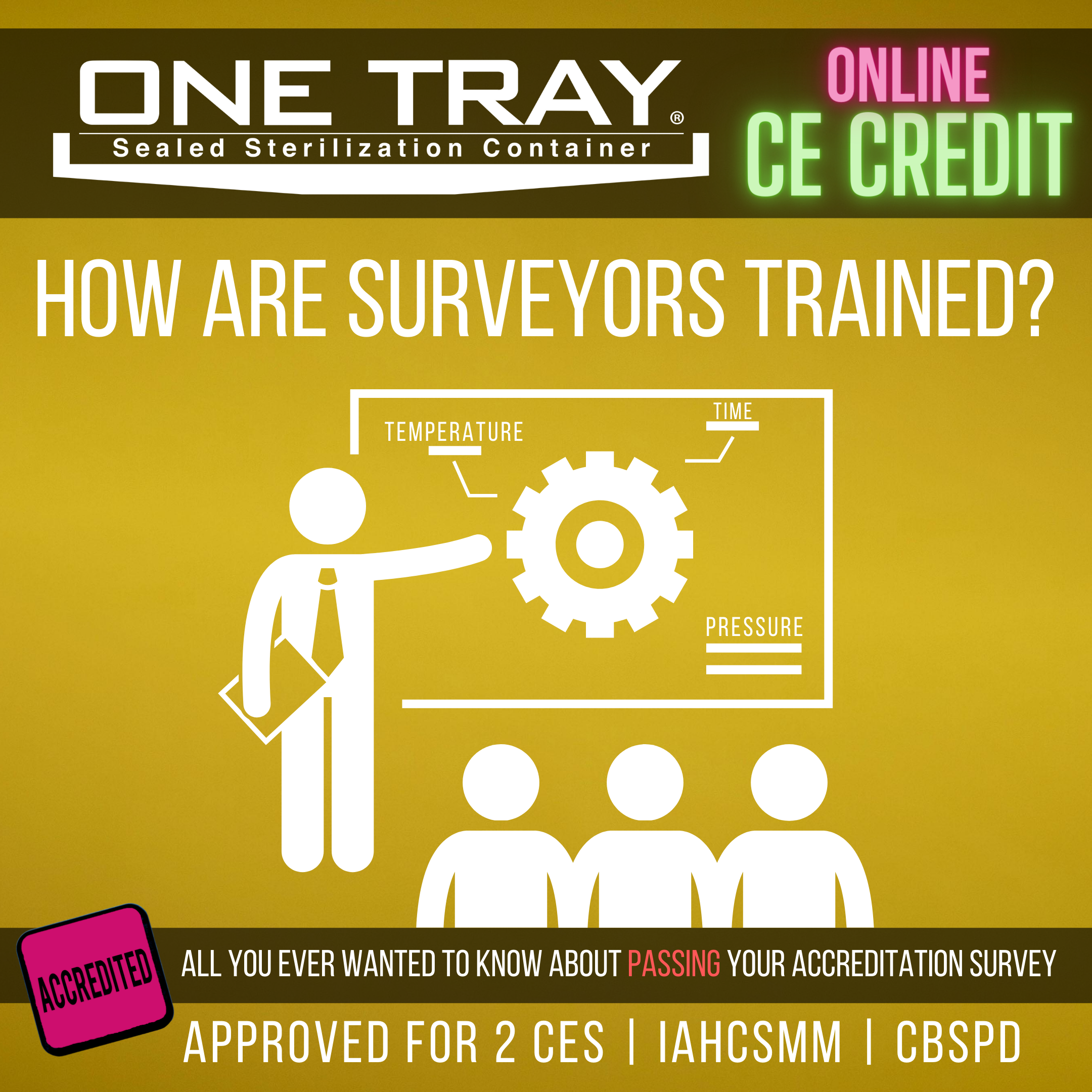
5. How Are Surveyors Trained?
Any surveyor could tell you that the responsibility for conducting a good Accreditation survey is no easy task. The broad set of information that surveyors are asked to be proficient in can be daunting. No matter how broad the experience of a surveyor, no surveyor is perfect. To help equip surveyors to be proficient, Accrediting agencies will put surveyors through some education and training in Infection Prevention, including some Sterilization and Disinfection. CMS has placed an increased emphasis on High Level Disinfection and Sterilization, and so surveys in Sterile Processing are becoming much more thorough than they used to be. Surveyors are equipped with an Infection Control Worksheet that guides them through key areas to look for, and they are given enough training to be dangerous.
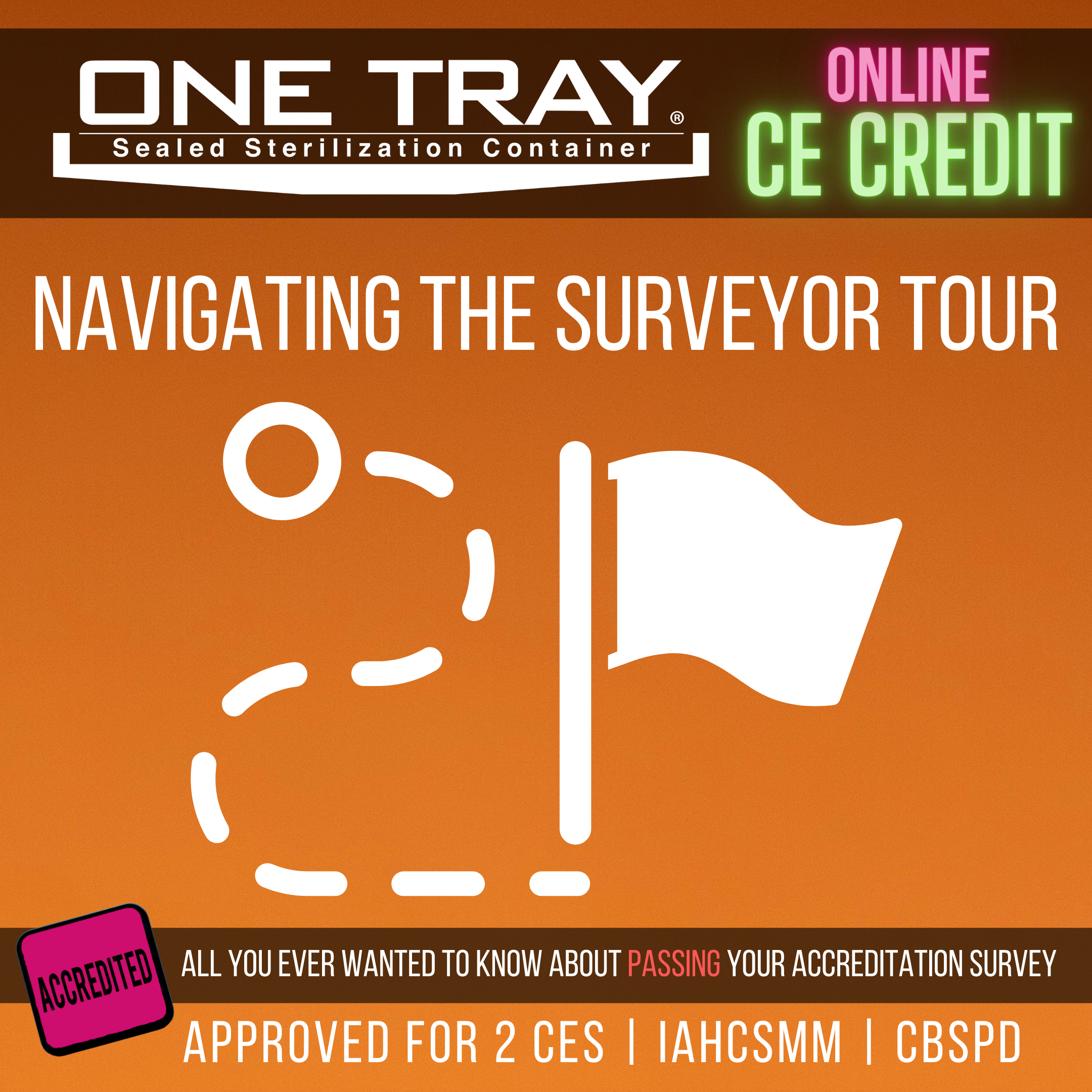
6. Navigating the Surveyor Tour
Whether or not your survey is announced and expected, the leader of the department or a designee will be contacted to speak with the surveyor and assist in guiding the tour of the department. Many surveyors will first want to speak with the department leader to introduce themselves, explain the purpose of their visit, and ask some initial questions about the department’s practices and functions. After this initial greeting and conversation, the surveyor is going to want to tour through the department to see processes and speak with staff members.
Many leaders wonder whether it is a good idea to lead the surveyor on the tour, or simply to follow and answer questions. This depends largely on the style of leader, and either approach is acceptable. If you choose to allow the surveyor to lead the tour, make sure that the surveyor is evaluating things that are factual and not opinion-based. This is the time to speak knowledgeably about your policies and procedures.
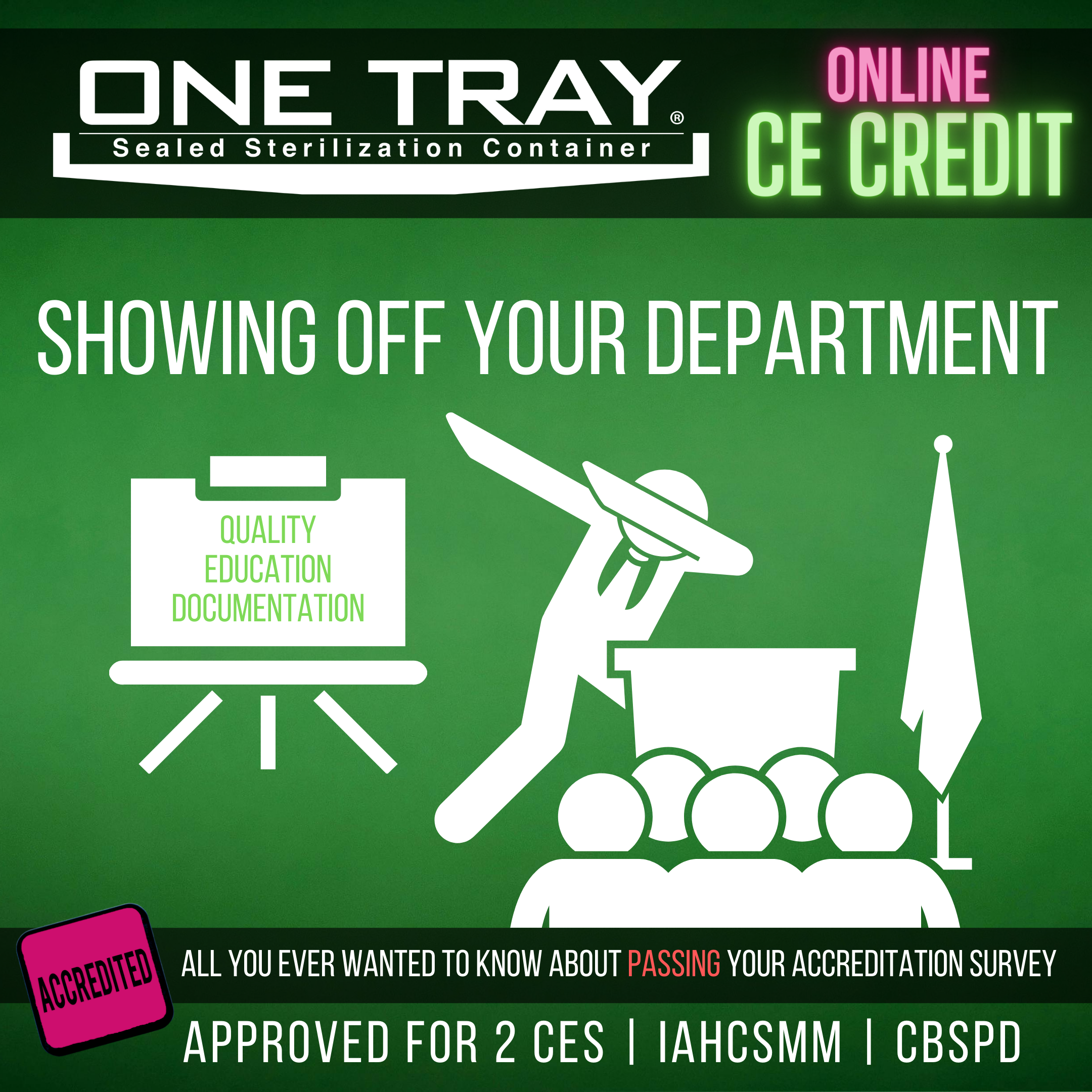
7. Showing Off Your Department
The goal of any department should be to operate in a way that would welcome a surveyor any day of the year. When the survey does come around, this is your opportunity to share knowledge with the surveyor and to proudly demonstrate what your team has accomplished. This means that when the surveyor arrives in the department, your team should not scatter and hide, but feel comfortable speaking with the survey about their work and training. They will feel much more comfortable doing this if the department is always operating “Survey-Ready” and they are not expected to speak to lots of brand new processes that were implemented to help the department pass the survey.
Remain confident in what you have accomplished in the department, stay on topic with the surveyor, and do not become frustrated or confused by the questions being asked. Give clear, concise answers to the questions being asked, and take the opportunity to highlight some of your department’s successes along the way.
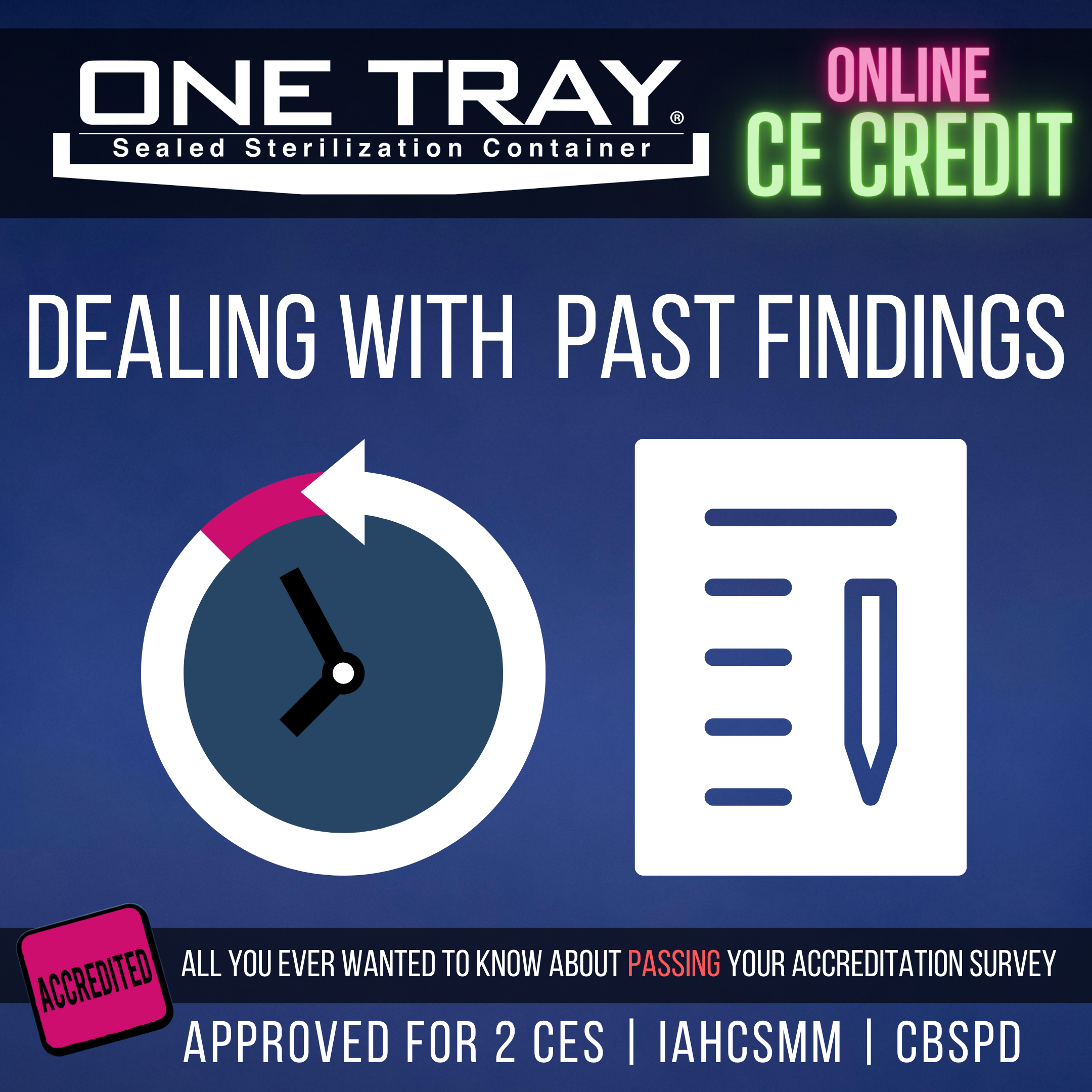
8. Dealing With Past Findings
When a surveyor comes to evaluate a department, the surveyor most likely will have reviewed the findings from prior surveys. Evaluating the department’s process for dealing with this previous finding will always be a priority for the surveyor during the survey. They will want to know that the plan of correction that was previously submitted is still being adhered to. If it is not, they will want to know what the cause of the change was. Perhaps the department developed a safer, more efficient method for correcting the problem, or a new product was purchased that changed the process.
Keep track of these changes and be able to speak to them. If you are new at your facility, it is a good idea to request a copy of the previous survey results to ensure that previous findings were appropriately addressed and those bad practices have not somehow slipped back into the daily practice.
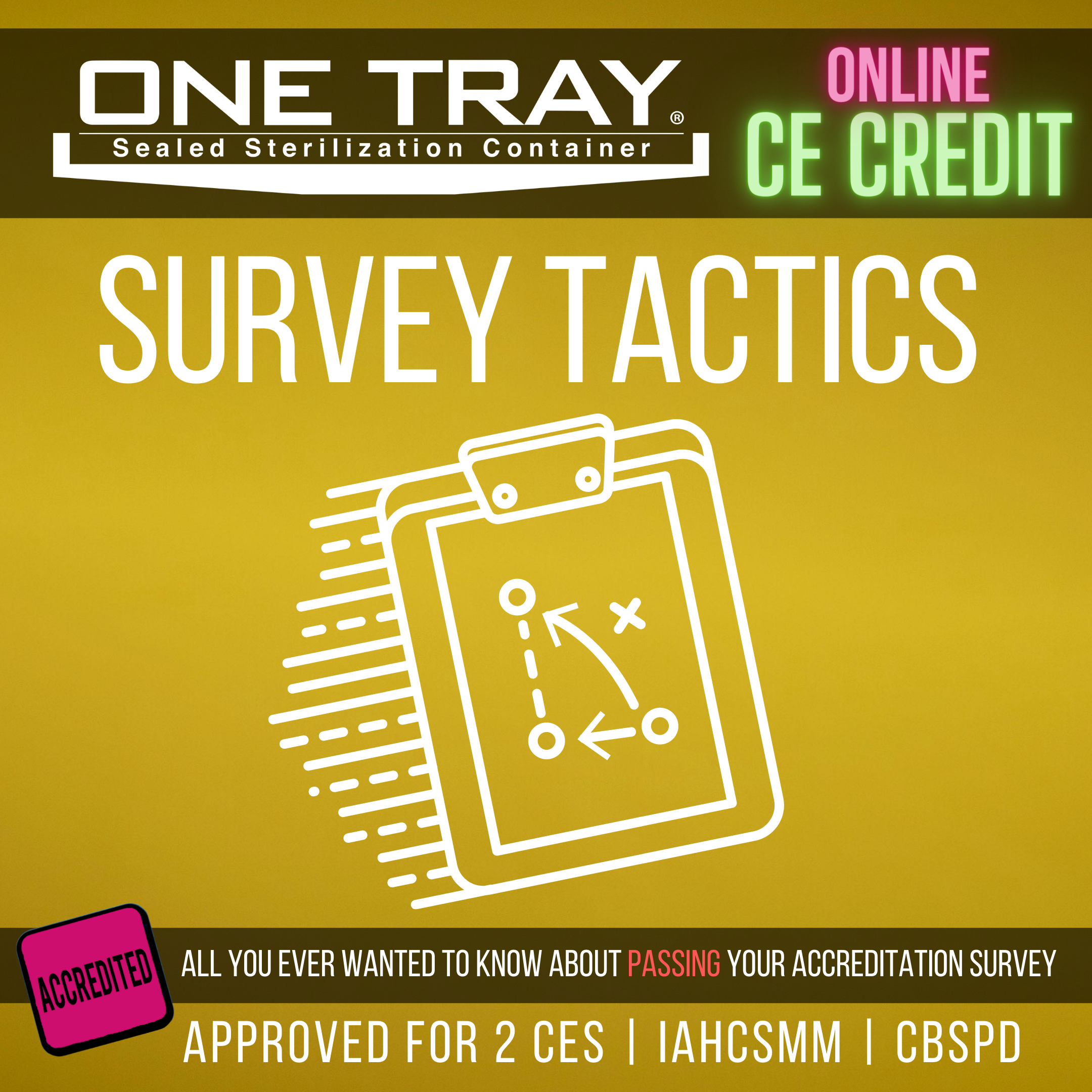
9. Survey Tactics
When conducting a survey, many surveyors will want to speak directly to the staff working in the department, and any employee is fair game. Surveyors are fully aware that departments put on their best face for a survey, and so they will talk directly with frontline staff about their daily work. Encourage your team not to scatter and hide when they see the touring group. Instead, make sure every member on your team is prepared to talk with the surveyors and is equipped to knowledgeably speak to your processes. Surveyors will be watching to see if what your team is saying matches up to work that is being performed in the department. If people give contradictory answers, or if a team member says something contradictory to the department’s written policies and procedures, the department can be cited for not consistently following best practices. Make certain that everyone is aware of the fundamental policies of the department, and that each staff member has a documented competency assessment (even temporary contract staff).
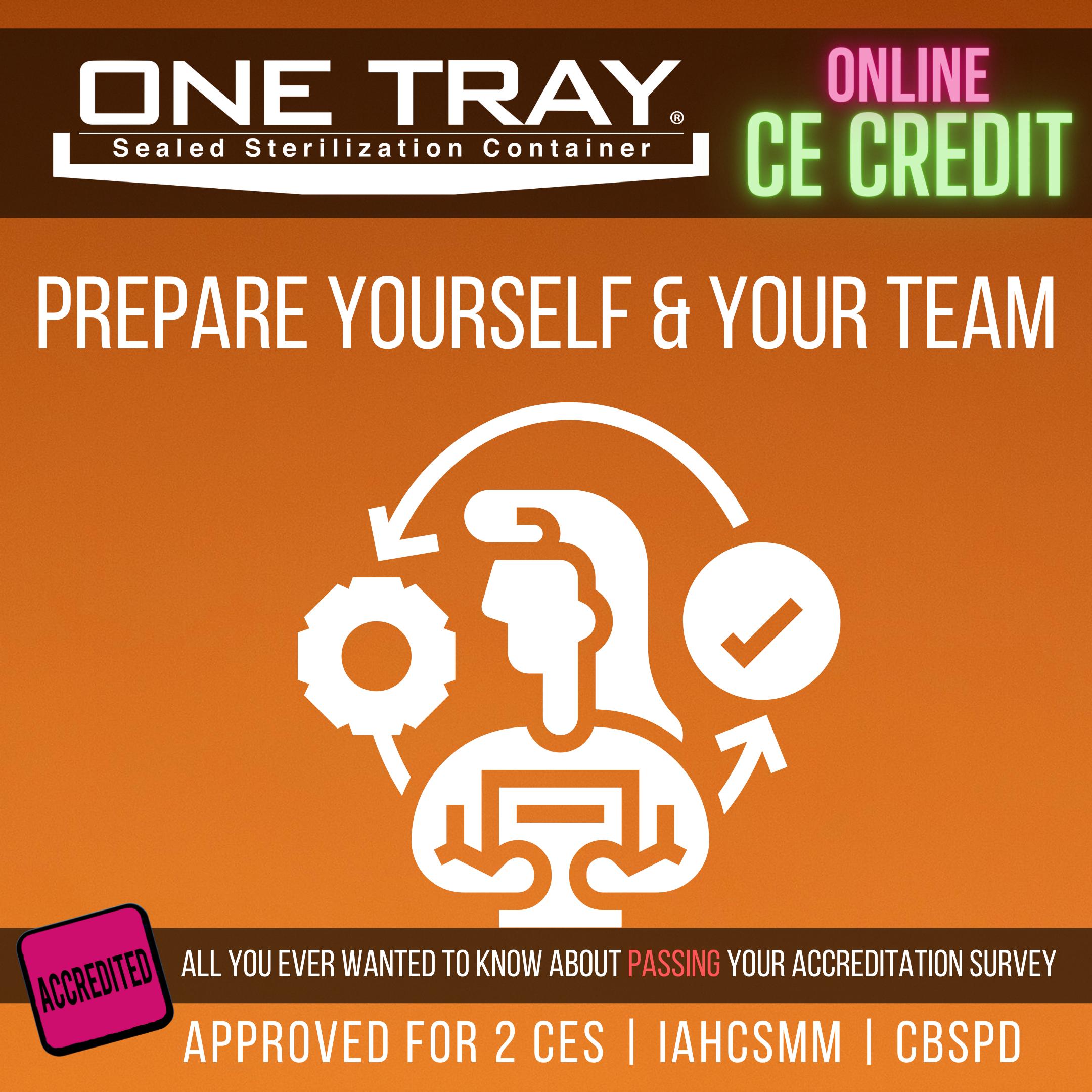
10. Preparing Yourself and Your Team
It can be intimidating for newer team members to have to talk with a surveyor. Here are some tips you can use to prepare yourself and your team for a survey:
- Be a good listener. Listen to specifically what is being asked of you, and answer only the question being asked.
- Ask for clarification. If you are confused by a surveyor’s question, do not be afraid to ask the surveyor to clarify what they mean.
- Ask for help. If the question is outside your sphere of responsibility, do not be afraid to ask a leader or peer. If someone is in training, they should be able to tell the surveyor where they would get that information (their trainer) if needed.
A helpful way to prepare your team is by performing mock surveys where you play the role of surveyor. Ask questions about the department’s processes and training. Acquire a checklist of industry best practices and observe if they are being consistently followed in your department.
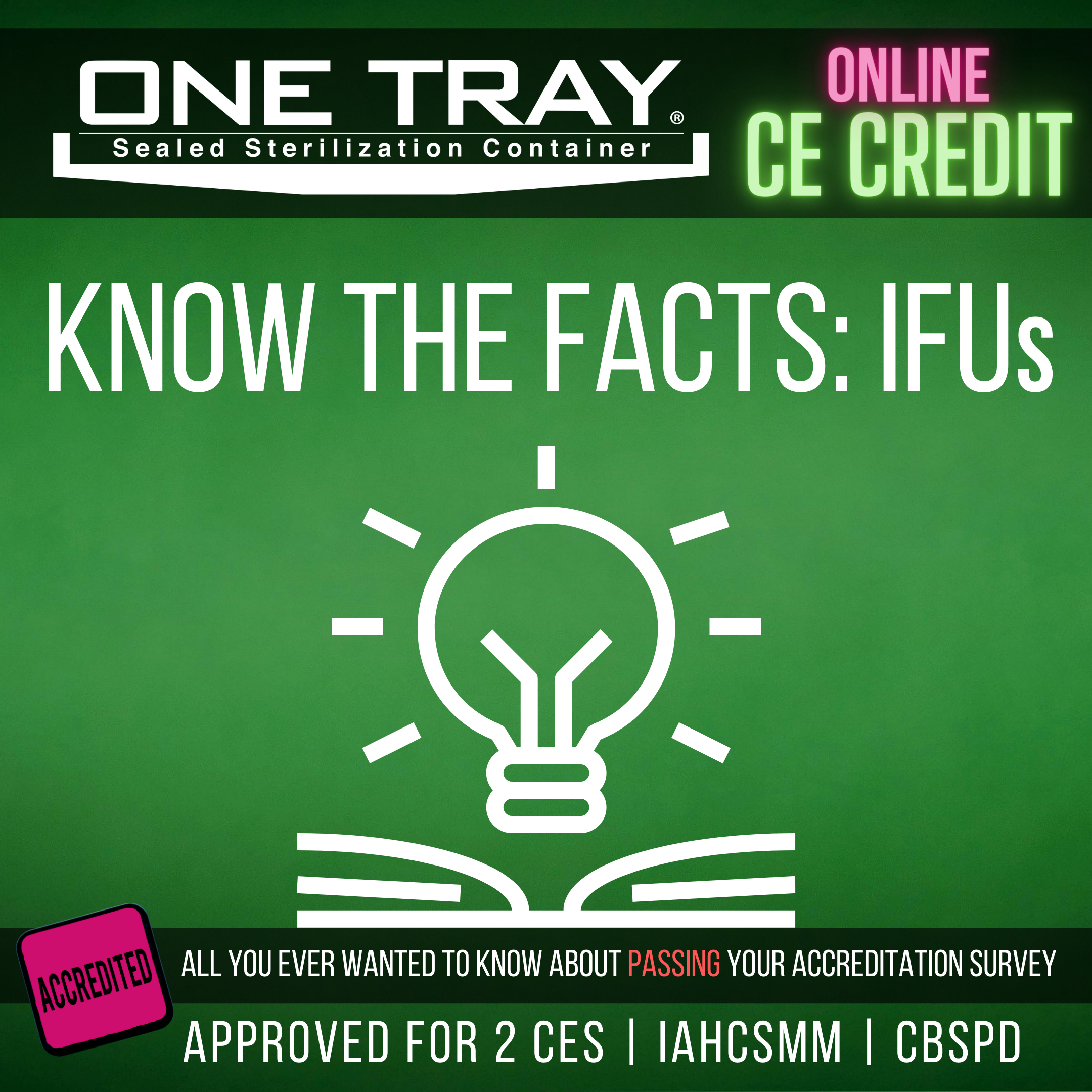
11. Know the Facts: IFUs
Device Manufacturers are required to provide Instructions For Use (IFU) with medical devices which outline cleaning, sterilization, and operation instructions. These IFUs are important documents for Sterile Processing because they outline the validated process that must be followed for a device to be considered clean or sterile. When surveyors observe your practices, they will want to see that devices are being cleaned and sterilized according to the manufacturer’s IFU. It is not uncommon for surveyors to request and read a device IFU to see if technicians are following all of the correct steps in processing. This means that your department needs to have access to those documents and that technicians are trained to be able to interpret in the information in an IFU. An important thing to note about IFUs is that they can be revised over time, so make certain that the department has the most current version on hand.
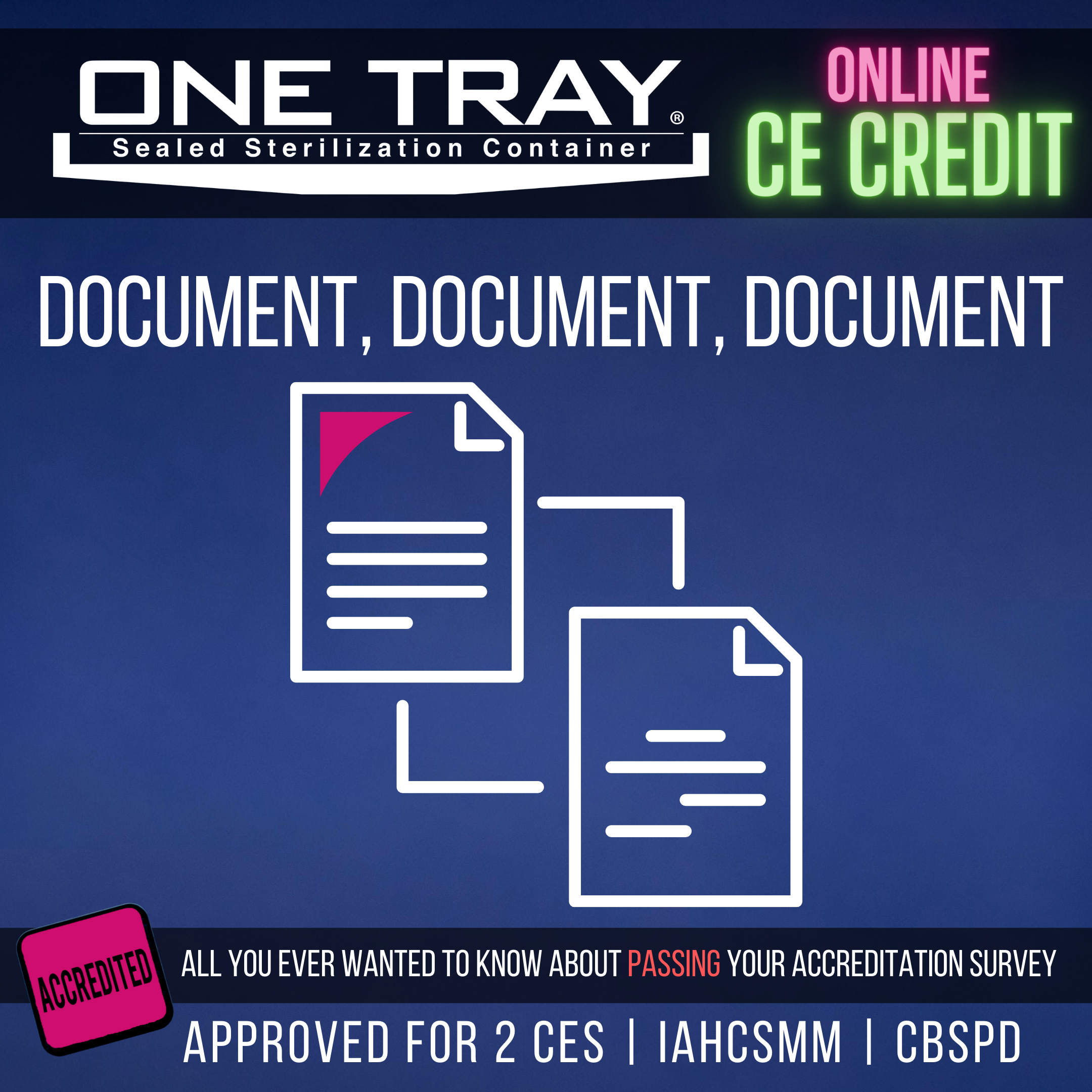
12. Documentation, Documentation, Documentation
The old saying, “If it isn’t documented, it didn’t happen” rings very true in Accreditation surveys. Without documentation of important functions in the department, you have no means of proving compliance to a surveyor. At the most basic level, this means keeping clear documentation of sterilizer records including the sterilizer printout, load contents, the operator ID, and indicator results. Other tasks in the department should be documented as well, including environmental temperature and humidity logs in the space, results of required equipment testing like washer verification tests, preventative maintenance logs for equipment, and logs for required cleaning of equipment according to the operators’ manual.
In addition to these department logs to be filled out by technicians, leaders should be keeping record of employee competencies, education being provided for technicians, and any documents related to holding technicians accountable to their responsibilities.
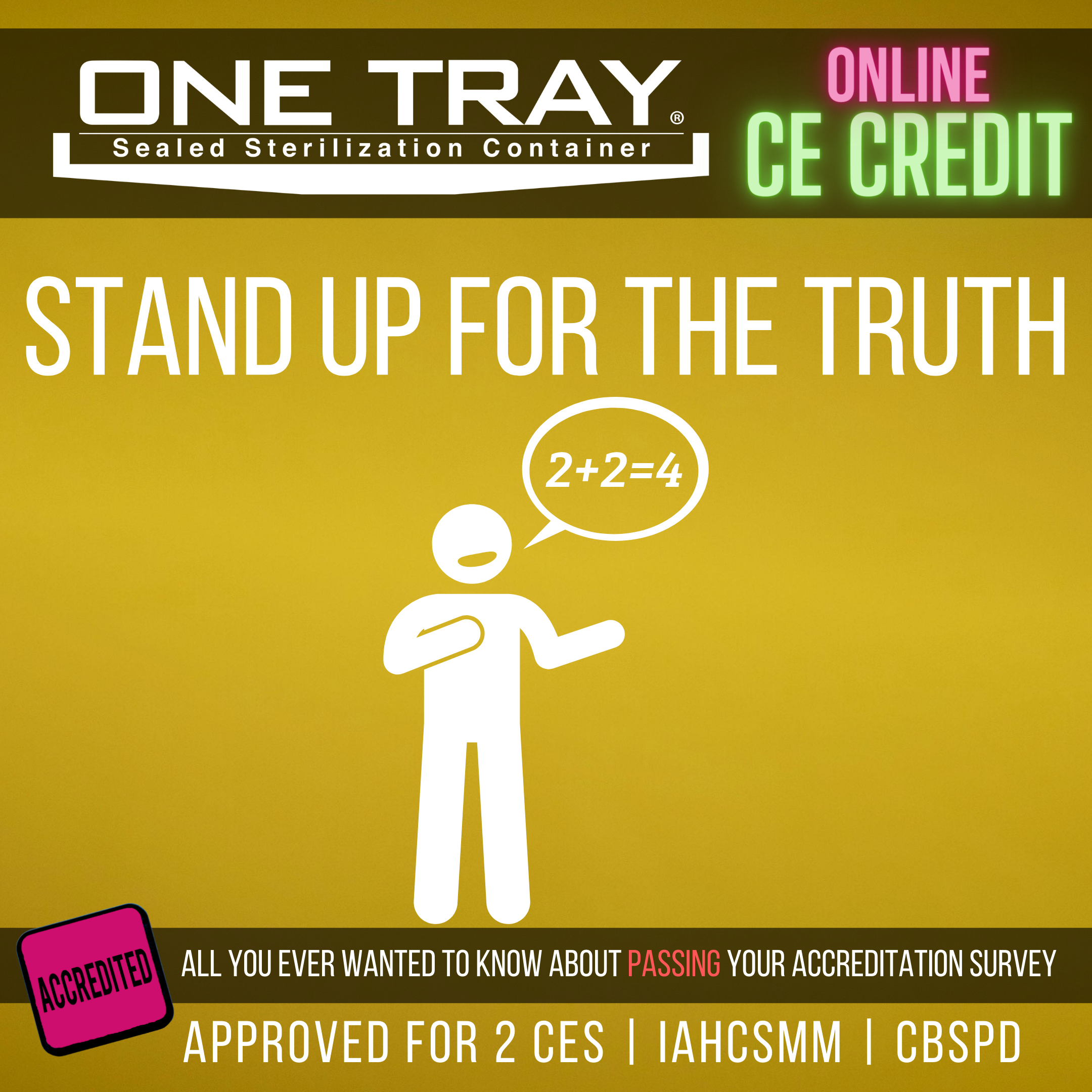
13. Stand Up for the Truth
No survey is perfect, because no surveyor can be perfect. No matter how much experience and knowledge a surveyor has, they can sometimes get the facts wrong. If you are being told something by a surveyor that you feel is in error, here are some tips for being able to address it.
- Always be respectful to the surveyor. Particularly when you need to be assertive and challenge the statement of a surveyor, it is important to remain professional and respectful.
- Remember that the facts will always win out in the end. Know the manufacturer’s IFUs, equipment operator’s manuals, and industry standards.
- A helpful way to disagree with the surveyor is to ask, “Can you please show me in writing where that reference is that you are citing us for?” Always approach this type of conversation with an open mind and a willingness to learn. There are many “grey” areas in Sterile Processing and the surveyor should be holding you to standards that can be produced in writing.
- If you end up with a deficiency that is not appropriate based upon the facts, the organization needs to submit in writing a challenge stating that the deficiency is not warranted and provide the rationale as to why it is not warranted.
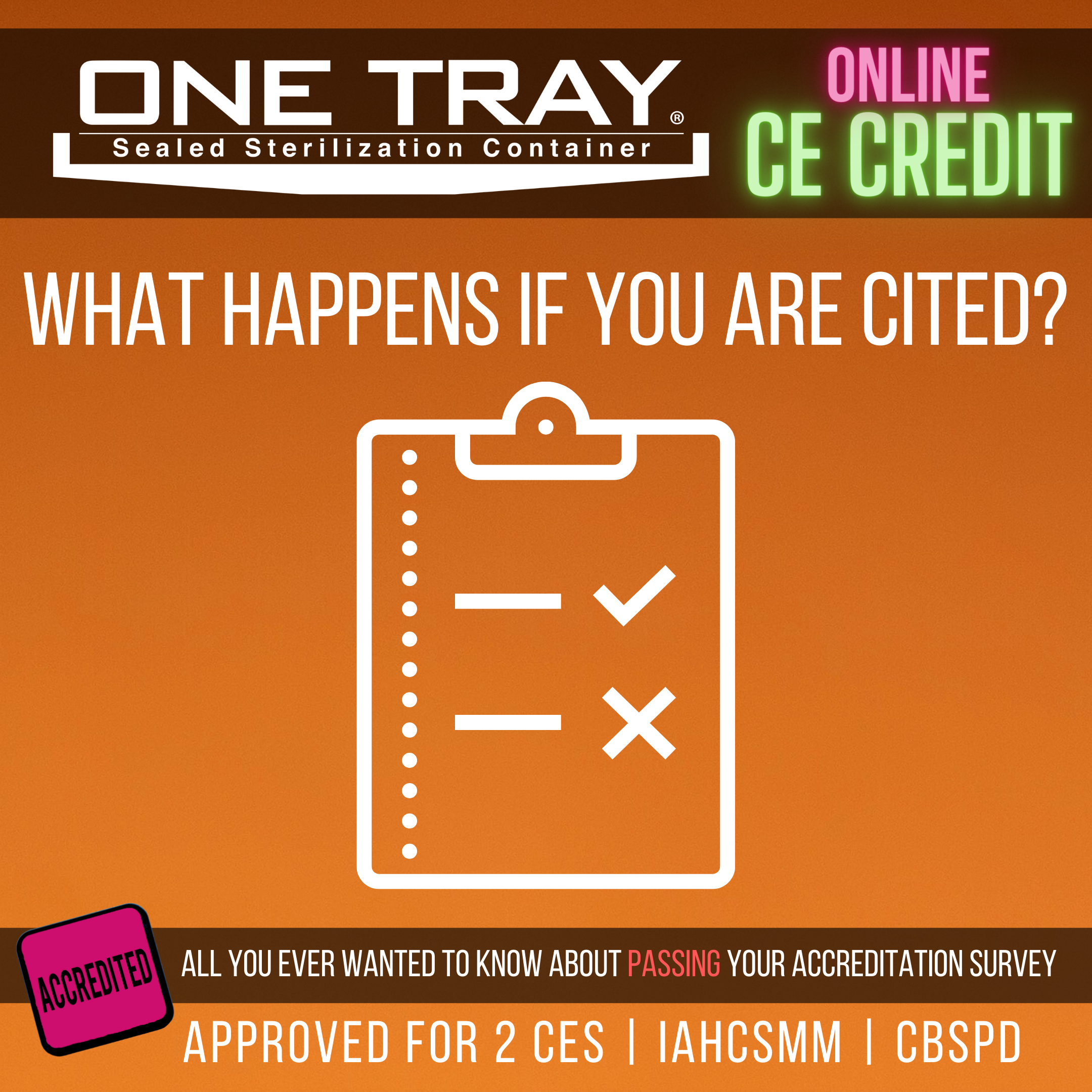
14. What Happens if You are Cited
If your department is cited for deficiencies, those deficiencies will be given in a list to the facility at (or after) the conclusion of the survey. It is typical that the facility will divide up that list of deficiencies to distribute them to their appropriate departments for follow-up. It is an unfortunate reality that the list of deficiencies provided by the surveying team does not include what went positively during the survey. Once you get your list of department deficiencies, you will be asked to come up with a plan of correction to submit to the surveying organization. It is a good idea at this point to share the deficiencies with the frontline staff. Sometimes they will have the best ideas of how to seamlessly resolve those deficiencies. Sharing the problem with the staff also helps them feel a sense of ownership over resolving the problem, and you are likely to get better cooperation and compliance in implementing the new process. Once your plan of correction has been written to address each of the deficiencies, usually an Administrator or Accreditation Department will send back the form to the surveying organization for review and approval.
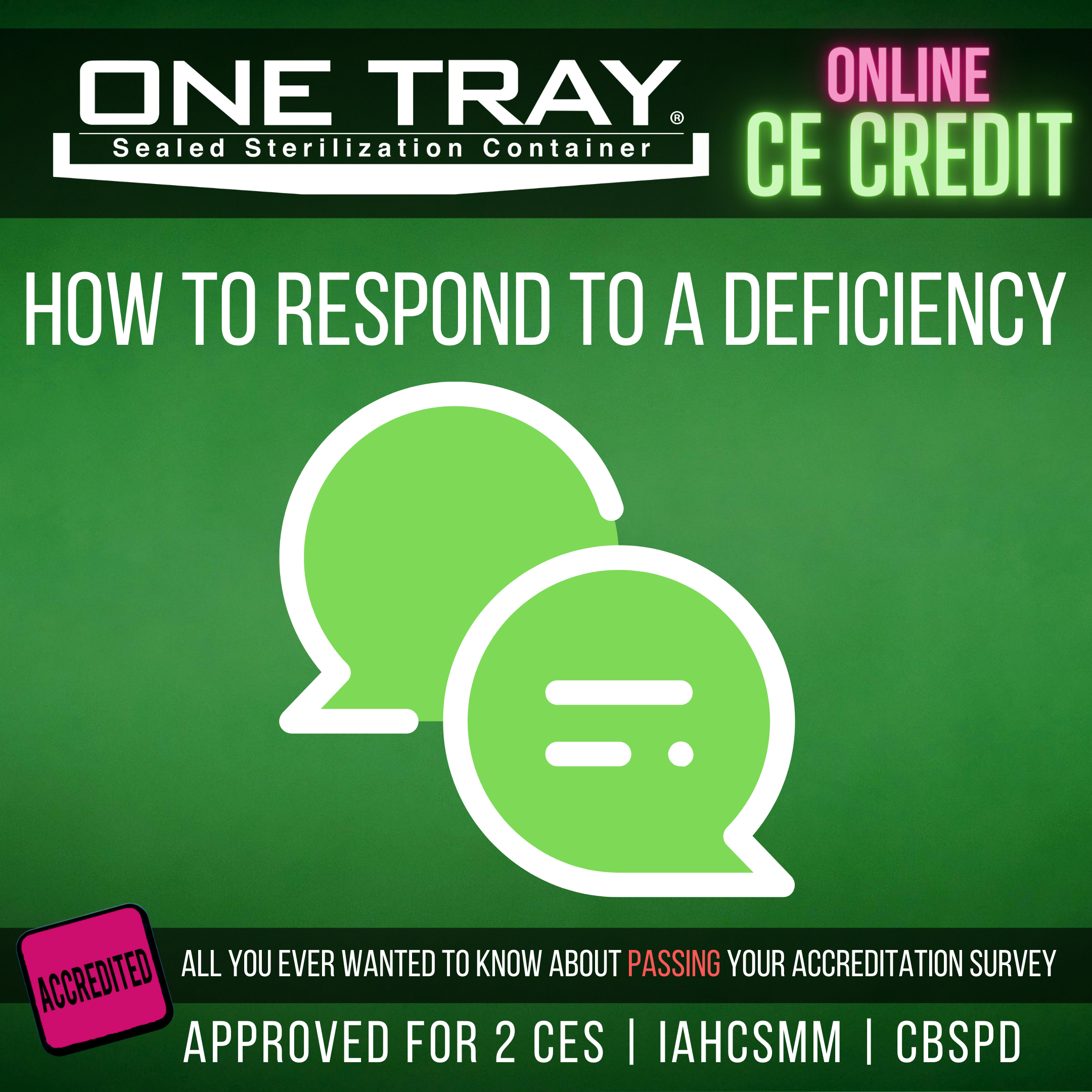
15. How to Respond to a Deficiency
If you receive a deficiency and are asked to write a plan of correction, these are some points that should be included in the plan of correction:
- What is going to be done? Clearly state the new process and how it will address the deficiency.
- Who is going to implement the new process? Make it clear who bears responsibility for completing the task.
- When will the issue be addressed? Including a timeline is important, especially if there will be a delay in implementing the plan.
- How will it be monitored? Include who will monitor the new process, including what steps will be taken address process failures.
- Always include education and training for the staff in the plan of correction. Sometimes this is all that is needed to correct the problem, but it should always be a part of the solution.